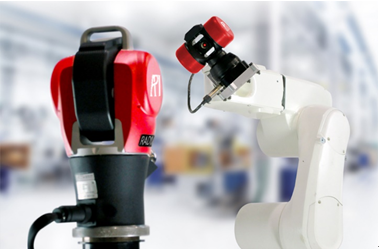
RPM模块(Robot Performance Measurement)
近年来,机器人产业在中国的发展可以用如火如荼来形容,国内机器人厂商不但在努力进入长久以来被四大家族(ABB,KUKA,FANUC,YASKAWA)统治的传统工业机器人市场,在新兴服务机器人行业、医疗器械以及3C行业也逐渐开始发力,市场前景非常广阔。API针对中国机器人市场的需求,适时推出了RMS(Robot Metrology Solution)系统解决方案。
RMS硬件核心为API激光跟踪仪Radian或OT2,同时支持多靶球方案和周边附件,如API主动靶标,最新款API智能靶标(6自由度传感器)。RMS软件为API美国团队自主研发,针对中国市场应用做了大量复杂而细致的工作,从而提供了市面最好的实用性。我们将从今天开始连载介绍API机器人解决方案的原理和优势,同时也介绍机器人性能评估,精度提高的方方面面。
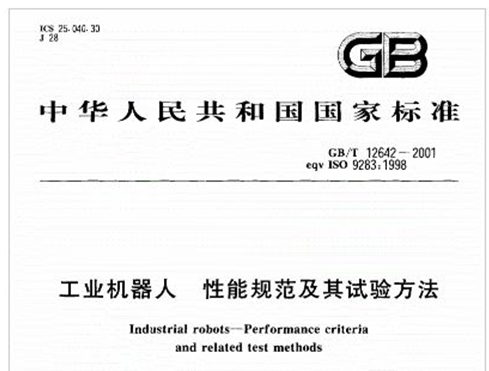
提到ISO9283标准,大家耳熟能详,该标准全称是“ISO9283:1998工业机器人性能规范及其试验方法”,对应ISO9283的国家标准在2003年更新了一次,全称代号为GB/T 2642-2013,实际上继承翻译了ISO9283:1998的全部内容,随着机器人行业的日新月异,这份机器人测量标准的地位越来越重要,成为评定机器人优劣的唯一评定办法。作为生产机器人测量设备和软件的企业。从今天起我们将分别对ISO9283:1998标准中的疑难问题,结合API RMS软件中的RPM模块进行深入解读。
1.测试立方体区域的选取的问题。
ISO9283试验方法的第一步,就是测试立方体区域的选取。一旦选定,机器人的运动和所有性能参数评估都在立方内部来进行,立方体中的任意两个位置点之间都可以直线到达,而该区域内相距最远的两个位置就是立方体对角线的两端;我们可以这样理解,机器人通常只会在一个尺寸远小于其臂展的有限区域内从事一项特定的工作,例如焊接和打磨,而不需要考虑距离较远的两个极限位置间的相对误差(例如第一关节旋转180度的情况),因为人们一般不会安排机器人在这样的工位上进行高位姿准确度(注意不是位姿重复性)要求的作业,那样的位置之间无法自由到达,无法按规划工作路径运行,因此没有太大实用价值(搬运码垛机器人会在极限位置间运行但通常只要求位姿重复性)。
API RMS软件关于确定试验立方体的思路是:在机器人基座坐标系下沿着向量(1,1,1)方向同时移动x,y,z,到达最大值位置,确定为顶点C1,然后再从C1沿着向量(-1,-1,-1)同时移动x,y,z,到达最小值位置,确定C7,从而确定立方体边长,检查立方体的各条棱边,如果机器人都可以直线方式全程自由运行后,就可以完全确定立方体的位置和尺寸大小了。由于翻译上的误解,人们往往把CUBE一词理解为正方体,而ISO9283也的确推荐了一系列正方体尺寸作为建议的试验值,实际上,机器人的工作尺寸在三个方向是不完全一致的,例如4轴SCARA(SelectiveCompliance Assembly Robot Arm)机器人,Z向为螺杆驱动,工作范围明显小于x,y向,此时显然不能要求x和y向的试验区域也保持跟z一样小,因此API RMS允许设置xyz三方向不同的边长。
RMS系统可以根据ISO9283标准,自动计算出试验立方体8个顶点的指令坐标值继而在试验对角面上缩减10%区域后计算得到五个测试点P1-P5的指令坐标值(其他具体各项试验中需要用到的试验位置指令坐标值也由软件自动生成)。
2. 测量系统和机器人坐标系对齐的问题。
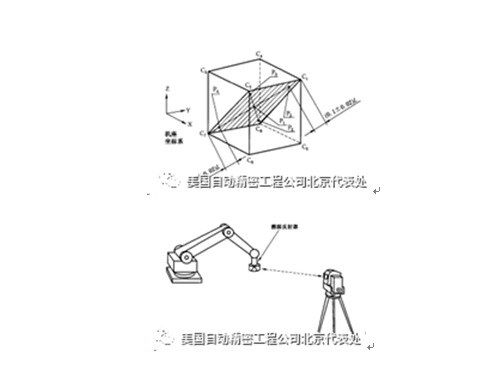
说到机器人的性能,人们首先关心的就是位姿准确性和重复性,在机器人控制器中输入一个指令位姿,机器人到达后,测量实到位姿,如此重复多次,再经过一系列统计学公式计算,就得到空间位姿准确度和位姿重复性指标。但问题是实到位姿由测量系统提供,测量系统一开始并不知道如何将测量系统的坐标系变换到机器人基座坐标系,这需要将测量系统对齐到机器人坐标系。
为了对齐测量系统,我们需要让机器人运行到若干个参考位置(通常是4个),记录参考位置的测量值(三维坐标),和指令值(同样是三维坐标),通过对这两组坐标进行最小二乘拟合,得到一个矩阵变换,有了这个矩阵,以后就可以将测量系统坐标系下的坐标值乘以这个矩阵得到机器人坐标系下坐标值,从而每个位置都可以与指令值进行比较,计算出位姿准确度和重复性,不难看出,参考位置的选取,会大大影响位姿准确度的结果,实际上我们评估的位姿准确度,就是P1-P5这五个点相对于参考位置的误差,因为参考位置用于对齐,也就被假设为没有误差(参考位置相互之间的相对误差则由最小二乘拟合计算包容),我们可以理解为用尺子去量一个长度时,用零刻度对准起点,在终点处读取长度,那么这个参考位置就是尺子的零刻度,如此说来,参考位置如果选在离测量点近的地方,位姿准确度结果就会小一些,而参考位置如果选择远一些,结果通常就会大一些。
一些厂商的ISO9283测试软件直接用P1-P5作为对齐参考点,这就相当于自己既做运动员又做裁判员,位姿准确度结果实际上得到的是P1-P5相互之间的距离误差,并非基于参考位置的绝对误差,另一些软件则是随意选取参考位置做对齐,这样得到的结果完全是随意的,改变参考位置,结果就完全不同了。其实关于参考位置的选取,标准中给出了原则,而且具体举例说明,就是说在测量平面为C1-C2-C7-C8时,用于对齐的参考点应该为与之相对的另一个对角面C3-C4-C5-C6。这样做可以完全体现出立方体整体的形状误差。
3. 动态性能规范的测量。
ISO9283:1998机器人动态性能规范包括以下几项
-位置稳定时间
-位置超调量
-轨迹准确度和重复性
-重定向轨迹准确度
-拐角偏差
-轨迹速度特性
-最小定位时间
-摆动偏差
a). 稳定时间和超调量的测量
标准推荐首先进行稳定时间试验,以保证在其他静态试验中测量系统可以正确等待足够的时间,获取机器人稳定状态下的数据。在API RMS软件中,由于硬件采样频率高达3000Hz,软件输出速率1000Hz,实时数据可以提供高动态性,可以精确计算出稳定时间和超调量,稳定时间的测量精度为1ms。稳定时间和超调量的设置中有两个重要输入参数,Limit Band和 Stable Band,其中Limit Band是标准中要求设定的机器人稳定指标,机器人末端位置变动小于这个Limit Band参数被认为达到稳定状态,Limit Band一般认为等于机器人厂家标称的位置重复性,例如标称重复性为0.03mm的机器人,Limit Band应该设置为0.03mm。
此外为了认定机器人当前位置是否达到最终稳定状态,API RMS软件引入了另一个输入参数Stable Band,因为Limit Band有时候数值偏大,即使位置变化小于Limit Band,机器人仍然持续一定的抖动,直接计算会导致最终稳态位置判断不准,从而影响超调量和稳定时间的计算。例如上图中,机器人最终稳定在0.02mm以内,如果Limit Band设置值为0.05mm,抖动从0.05mm衰减到0.02mm期间的数据会被计入最终稳态位置(取平均),影响最终结果。Stable Band反映的是测量系统读数被机器人自身刚性、环境条件及其他外界因素影响而导致的本底噪声。Stable Band 数值必须小于或等于Limit Band数值。
b). 重定向轨迹准确度
重定向轨迹准确度的试验轨迹是穿过立方体中P1点的一段水平直线(P6-P9),重定向的含义是指机器人末端中心保持在直线轨迹上,但是运动过程中必须连续动态改变姿态角。这也是所有14项ISO9283试验规范中唯一需要改变姿态角的试验,旨在考核机器人对姿态角动态控制的性能优劣,在喷涂和打磨这一类对姿态角要求较高的应用场合尤为关键。这项试验同时要求测量系统能够精确标定出工具中心点,由于姿态角变化,工具不再是平动,工具中心点的标定误差会直接导致轨迹误差。
一般机器人标定工具中心有一点法和四点法,其原理都是用实际工具的端去对齐一个固定针尖参考点,一点法通过一个已知工具来传递参考点位置,多点法则通过多方向对齐参考针尖,求解计算出参考点位置,二者都要求用目测方式来物理对齐工具中心,不仅有很大人因误差,而且受限于工具尖端和考点尖端的形状误差。对于激光跟踪仪系统来说,完全没有必要这么繁琐,API RMS可以用绕工具中心旋转,连续跟踪目标的方法,精确得到当前工具中心完全避免了人目测对准带来的误差。差
c). 拐角偏差
拐角偏差试验实际上包含两类拐角方式,一类为尖锐拐角,机器人在执行直角转向轨迹时,要求到达拐角时速度降到零,然后在离开拐角方向上从零开始加速,检验机器人的加减速控制性能,另一类为圆弧拐角,为了保证机器人工作的平稳,在直角拐角处,指令控制机器人划出1/4圆弧过渡,需要评估实际过渡圆弧半径和指令中给定的圆弧半径之间的偏差。综合起来都是检验机器人运动学控制性能。拐角偏差试验对测量系统的高速采样性能提出了很高的要求,由于机器人速度通常达到2米/秒,一些采样速率较低的硬件系统无法获取轨迹上足够密集的样本,对拐角偏差结果的计算会带来很大的影响。API RMS系统的1000赫兹数据传输率,是目前市面上采样率最高的机器人测量系统。
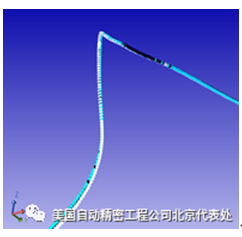
d). 轨迹速度特性

e). 最小定位时间
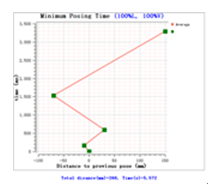
f). 摆动偏差
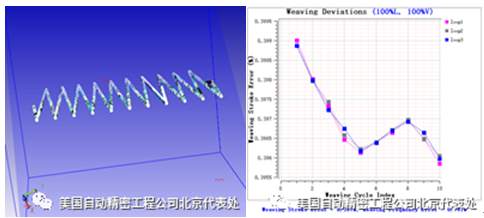
4. 静态性能规范的测量。
-位姿准确度和位姿重复性
-多方向位姿准确度变动
-距离准确度和距离重复性
-位姿特性漂移
-互换性
-静态柔顺性
API RMS同时支持多靶球测量方案和6维智能靶标。其中的多靶球六维测量方案可以提供最大的经济性。6维智能靶标则提供高效率和便捷性。
使用多靶球时,其中一个靶球被设定为工具中心点,可以进行所有动态性能试验,并提供位置信息,另外两个靶球用于计算机器人末端姿态角信息,如果使用6维自动靶标则可以在一次测量中得到所有的位姿信息。API RMS通过检测机器人运动停止状态,触发记录数据,自动完成所有形态试验项目,一旦开始试验就不再需要人为干预,可以自动完成后续测量。对于一些生产线上的自动化测量需求,用户可以定制可选的机器人通讯接口,通过IO信号来控制机器人和测量系统之间的同步协调,实现全自动测量。
a). 多方向位姿准确度变动。
多方向位姿准确度变动要求机器人在每个试验位置都以x,y,z三个方向进入,测量机器人实到位姿的变动(不是和指令位置进行比较),需要注意的是机器人的运动路径仍然不能超过立方体的范围,因此,如果所有测量点都应该从立方体的中心由内而外进入试验位置。
b). 位姿特性漂移
位姿特性漂移只选用一个试验位置(通常是立方体中心点P1),长时间观测机器人到该位置的位姿变化,标准建议的试验间隔周期为10分钟,每次记录重复10个循环。在10分钟间隔时间内,务必保持机器人处于热机状态,为了操作方便,一般编程控制机器人从P2点向P1点运动70%行程然后返回P2,并不到达P1点,以免误采数据。由于一些机器人控制器不支持较长时间的定时器指令,API RMS中10分钟间隔由测量系统电脑控制计时,当时间满足10分钟,并且机器人也回到P1点时,软件才会开始新一轮记录(10个循环)。
c). 互换性
互换性是指机器人在发生故障需要更换的情况下,新的机器人安装在同一机械接口上,在不重新进行工作场景标定的情况下,所能达到的位置准确度的一致性。它主要反映多个机器人基于其机械安装接口的位姿准确度的一致性。包括机器人基座,以及工具接口的机械重复定位性能。需要注意更换机器人以后,需要将装有靶球或测量靶标的工具,整体原封不动安装在新机器人的末端接口上,并用定位销保证对中且安装方向一致。
d). 静态柔顺性
静态柔顺性试验需要设计专门的加载装置,对机器人末端施加指定的负载,通常可以利用滑轮机构和砝码来控制力的大小和方向。进行这一试验时,必须用指令控制机器人到达试验位置,伺服处于打开状态,所有关节不得掉电抱闸。
以上结合API RMS 系统中的RPM模块介绍了ISO9283试验中大家关心的一些问题,我们在下一期中会结合API RMS系统中的DH模块介绍关于机器人DH参数校准和补偿应用的知识。
相关新闻:
API邀您共聚2025慕尼黑上海光博会
2025慕尼黑上海光博会 慕尼黑上海光博会是德国慕尼黑博览集团在上海举办的激光、光学、光电行业的专业展览会,其影响范围依托中国,辐射亚太、东南亚、中东及全球,是
Radian激光跟踪仪在风力发电机 门架检测领域的应用
对风力发电机门架测量领域的探索 风力发电机门架是构建风力发电机支撑部分最重要的核心组成部分:具有尺寸长、宽度小、待测特征因焊接件极易变形等复特点,极易造成门机架
API科技产品为人形机器人核心部件研发与制造 提供测量技术支撑与数据精准保障
继2025年2月12日期中国中央电视台 “新闻联播” 栏目中播报的《关于中国机器人产业发展》的相关报道中展示了API品牌Radian激光跟踪仪在工业机器人与人形
了解更多:
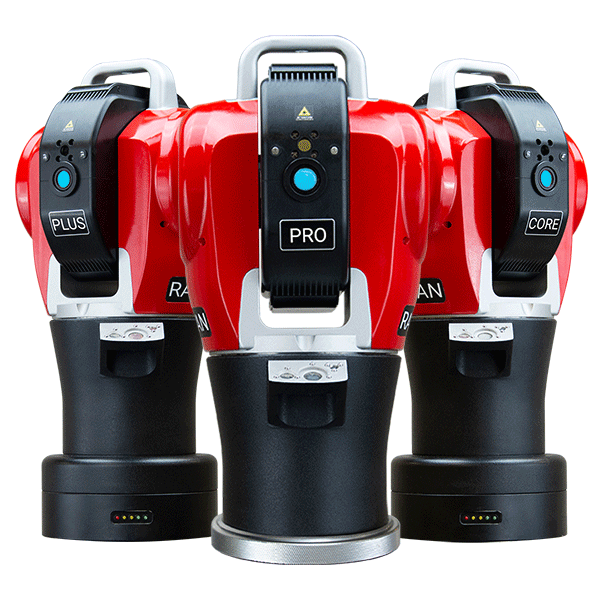
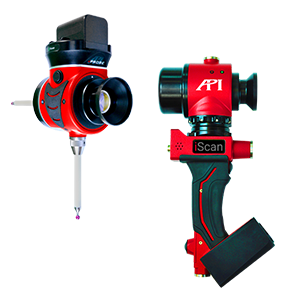
激光跟踪仪靶球&测头
Maximize laser tracker productivity with hand held and 激光跟踪仪主动靶标.
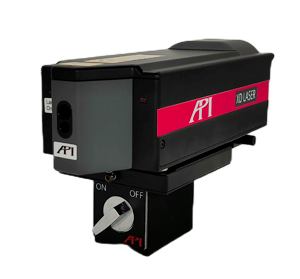
XD Laser CMM Calibration
The XD Laser is the only assessment system that can measure all 6 error parameters simultaneously in a single set-up
了解更多 /xd-laser
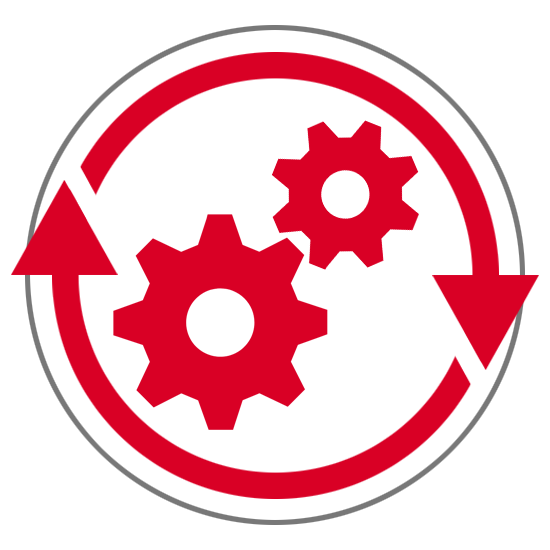
API Reverse Engineering Service
Reverse engineering services include scan as-built parts to creation of a 3D digital point cloud and CAD Model.